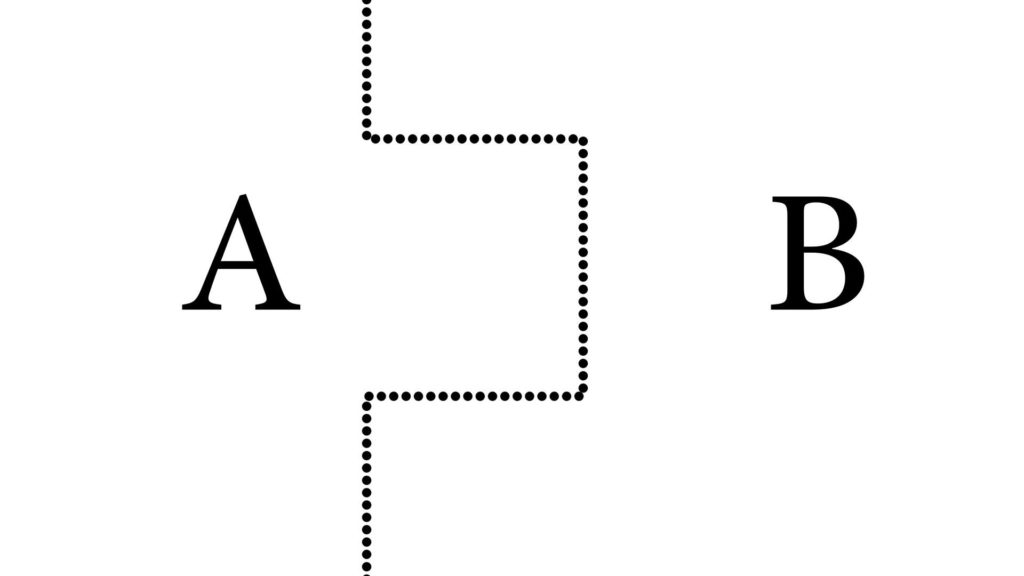
Error Propagation During the 3D Scan
A 3D scan is made of two parts that fit together perfectly like a puzzle. Part A and part B. Our example 3D scanner has an accuracy of ±1 mm. This means that after the 3D scan of part A, the resulting 3D model could be 1 mm larger or smaller than the original. The 3D model of part B could also be 1 mm larger or smaller after the 3D scan. This means in a worst-case scenario, the whole puzzle is shifted by 2 mm and does not fit together properly.
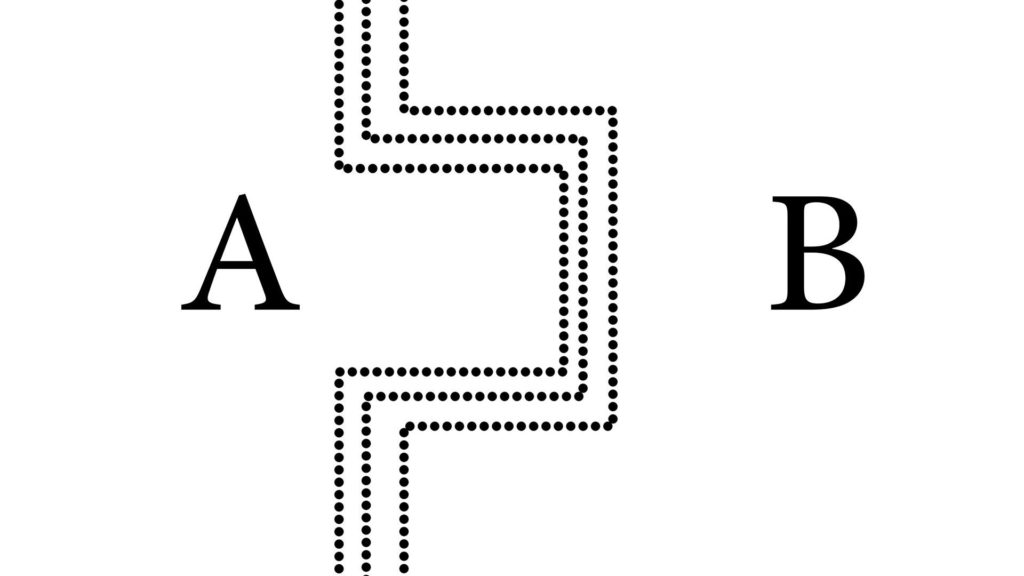
Error Propagation in Reverse Engineering
After the 3D scan, we perform reverse engineering with parametric modeling and a history tree. This has an average deviation of up to ±0.25 mm from the original 3D scan. Adding the deviations of both processes, the puzzle may be off by 2.5 mm.
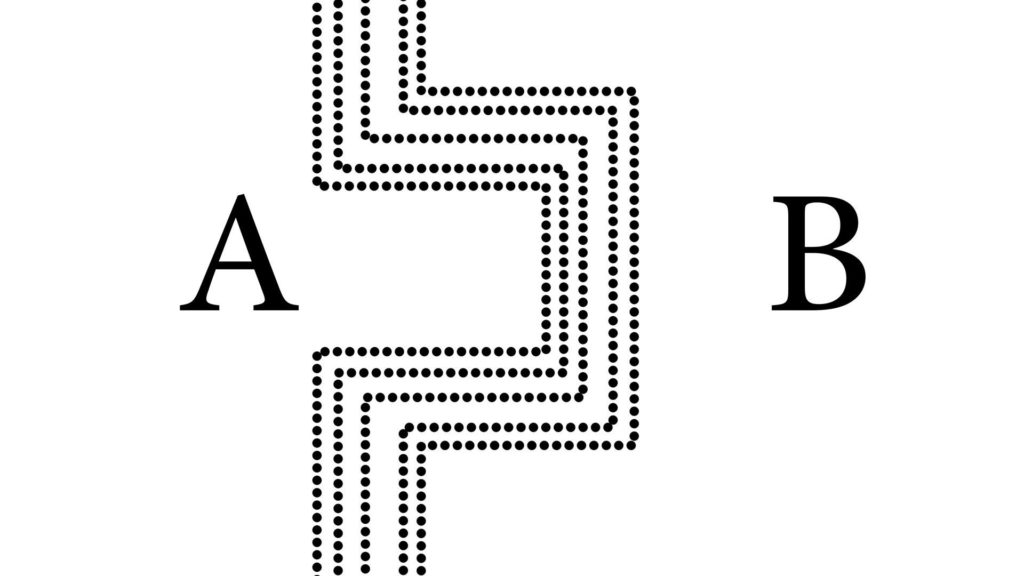
Error Propagation in Manufacturing
During the last step, the 3D model is manufactured with metal 3D printing. Due to manufacturing deviations, the parts may be produced 0.2 mm larger or smaller. In a worst-case scenario, part A and part B now have a combined total deviation of 2.9 mm, and the puzzle pieces no longer fit together.
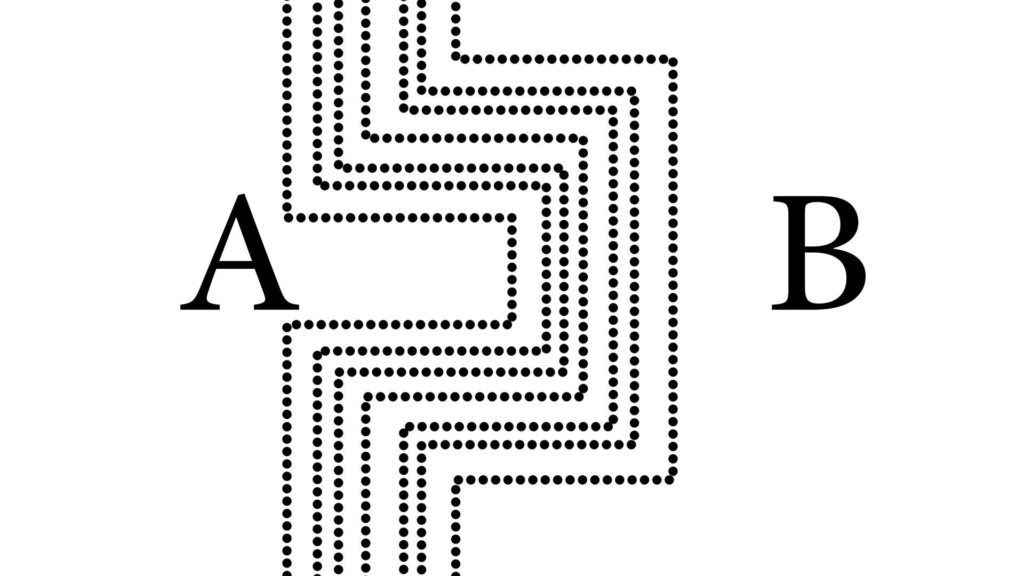
Conclusion
It is not possible to eliminate error propagation in reverse engineering, but it can be minimized. At each step of the reverse engineering process, it is important to choose the method that has the least deviation. Therefore, the most accurate 3D-scanning technique should be chosen. And for the reverse engineering process, it is up to the engineer to work as precisely as possible. There are also manufacturing processes that are more precise than others. For example, CNC milling is more accurate than 3D printing.
May we advise you on how to mitigate error propagation with your project?
Holocreators offers professional 3D-scanning and reverse engineering services. We would love to help you with your project and advise you, for example, on how to minimize deviations in your reverse engineering project. Please call us at +49 40 481133 or send an email info@holocreators.com